|
Synthèse tirée en grande partie des 2 ouvrages de
Pierre-Lucien Pouzet :
- Histoire de la Société de Paris et du Rhône
- La Grande Aventure automobile lyonnaise
et avec les souvenirs de messieurs : Bono, Duroux,
Charras, Mazzorana et Montherrat
Par Maurice Charras
En 1915
était créée, à Villeurbanne sous l’impulsion d’Emile Girardeau, la Compagnie Industrielle de Paris et du Rhône qui devient en 1916 la Société de Paris et du Rhône. Elle édifie, sur un terrain de 2.5 hectares, une usine
située 41 chemin de saint Priest (avenue général Frère) et rue de l’Asile
(rue professeur Morat). A l’époque l’avenue Mermoz n’est pas percée. L’usine se
construit au milieu de terres, jardins, remises, vergers,
poulaillers.. En 1925 le terrain s’étend jusqu'à la rue Bataille, sur
6 hectares. Les premières fabrications consistaient exclusivement en un
matériel radioélectrique pour l’armée : postes portatifs de campagne,
amplificateurs à lampes…Les effectifs avoisinaient les 800 personnes en
1918 et des ateliers d’isolants et de fonderie furent construits. La guerre
terminée les fabrications radioélectriques pour l’armée diminuent et rejoignent
progressivement la société mère la Société Française de Radioélectricité. Une
sévère période de reconversion allait s’ouvrir.
C’est vers
l’industrie automobile que se dirige la société avec la création en 1918 d’une
dynamo-démarreur appelée dynamoteur qui fut adoptée par de nombreux
constructeurs : Voisin, Talbot, Bugatti, Berliet. En même temps la
construction de dynamos et de démarreurs se développe pour de plus grandes séries
chez Peugeot, Simca, Panhard et Levasseur, Berliet, Cottin Desgouttes…
Lancement
en 1925 du célèbre aspirateur « Aspiron » avec la publicité du groom
en livrée, très novatrice pour l’époque. L’effectif atteint 600 personnes.
En 1938 les bâtiments couvraient 20 000 m² avec 850
personnes et une production de 16 000 aspirateurs et 65 000 dynamos et
démarreurs. Création d’un atelier d’ébonite. L’ébonite est un
caoutchouc durci par un fort ajout de
soufre. Cet atelier se développera, après la guerre pour devenir le
département « Isolants ».
Pendant la guerre de 39/45 les fabrications s’écroulent et
apparaissent quelques voitures électriques (environ 150), des éoliennes de 300
à 1200 watts, à fabrications
confidentielles, ainsi que des ventilateurs pour gazogènes. En mai 1945 les
effectifs sont de 460 personnes et il faut attendre 1947 pour que la production
redémarre.
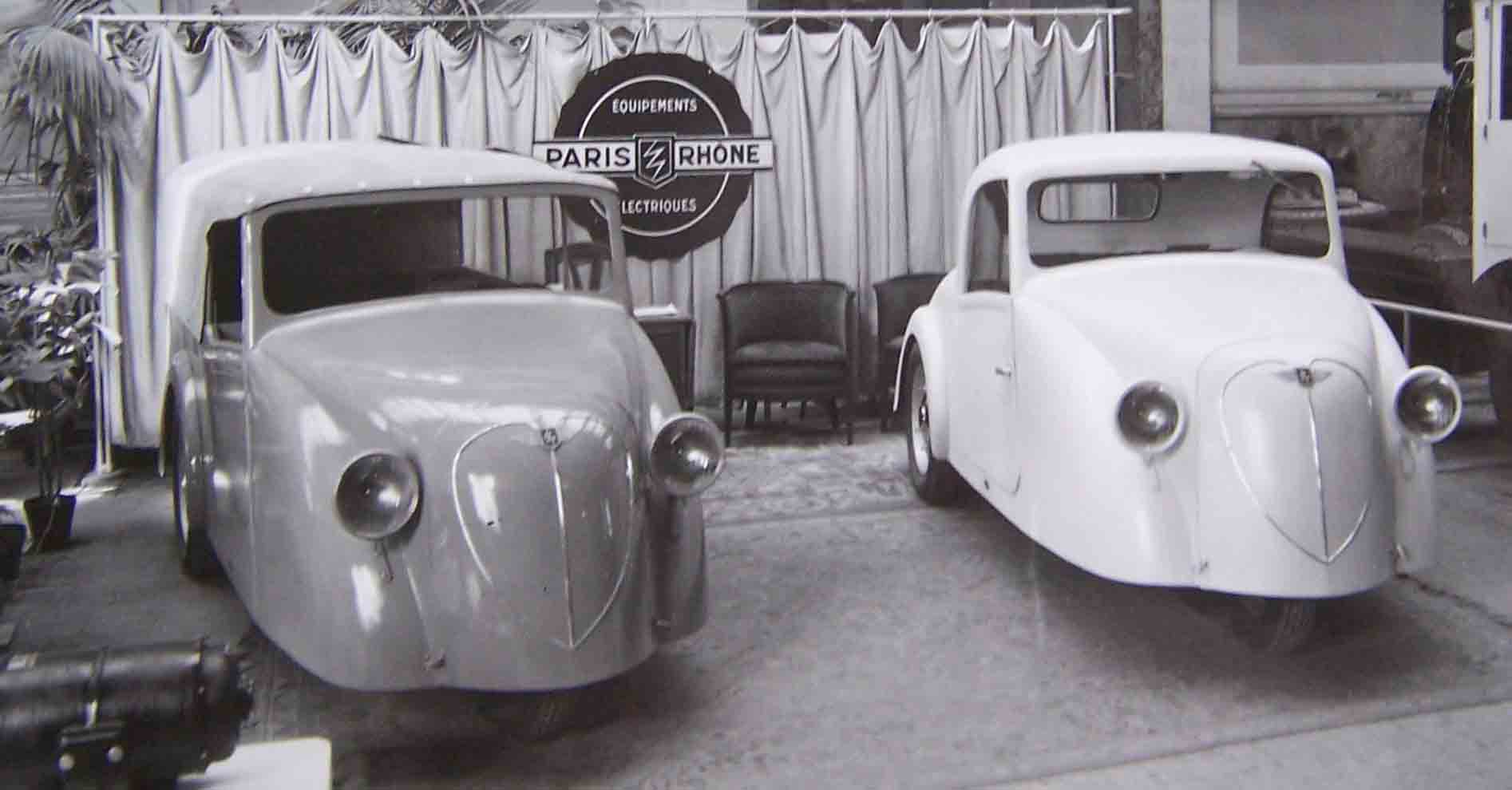


Une période de grande expansion s’ouvre, il faut augmenter
les surfaces de production :
1952: construction d’un grand bâtiment sur 2 niveaux de 5 000 m2 pour
le département des Appareils Ménagers dont les principales fabrications sont
les aspirateurs ménagers et industriels, les cireuses, et les moulins à café
avec le broyage du café par un système à noix ayant le même principe que les
anciens moulins manuels. Les amateurs de bon café étaient de fervents adeptes
de ce système qui permettait d’avoir un
café délicieux.
1958: Construction d’un nouveau
bâtiment de 5 000 m2 sur 2 niveaux, destiné à la production des équipements des
poids lourds.
1961: Mise en service du bâtiment
administratif du 36 de l’avenue Mermoz ( 3 500 m2 ) qui existe toujours.
Dans les années 1960/1970 les
régulateurs étaient assemblés dans une mezzanine, sous les sheds d’un atelier.
Dans les étés particulièrement torrides, la chaleur devenait intenable et l’on
compta certains jours jusqu'à 30 ouvrières transportées en civière à
l’infirmerie.
1962: Apparitions des alternateurs
qui vont bientôt supplanter les dynamos.
1965: Achat de l’usine Astra au 62
de l’avenue Mermoz où sera implantée la production de régulateurs électroniques
et ensuite le centre d’apprentissage.
1966: Création du centre de
recherche Béthenod, et réalisation d’un passage souterrain, sous l’avenue
Mermoz qui permet de relier les 2 usines.

1965: Location d’un magasin de 5
000 m2 à Saint Quentin Fallavier : liaison par navettes.
1966: une politique d’exportation commence à se développer avec des
prises de participation chez Mototrans à Barcelone, Sahney en Inde en 1971,
Famelec au Maroc en 1972.
1967: Construction d’un magasin central de 5 000 m2 dans la partie
nord.
1968: Achat
de l’usine « La Soupape » de 10 000 m2, situé au 37/39 rue Maryse
Bastié et impasse Pomone où sont transférés les Appareils Ménagers. Les grèves
sont rudes avec occupation des usines: partie par l’encadrement et partie par
les ouvriers. Elles se termineront les dernières de la région lyonnaise, avec
l’acquit de la 5° semaine.
1969: Les
besoins de surfaces de production supplémentaires amènent la Société à
absorber la société FAR (Fonderies et
Ateliers du Rhône) à Villeurbanne qui produit du matériel de cuisson :
cuisinières à gaz et électriques, et des radiateurs de chauffage à gaz.
1970: Les Appareils Ménagers sont transférés chez FAR, l’atelier de
Maryse Bastié est spécialisé dans la fabrication des alternateurs. Cibié et Paris-Rhône font un mariage de raison pour éviter que
l’actionnariat de Cibié qui est très
dispersé passe sous une coupe étrangère. Ferodo prend le contrôle de
SEV-Marchal, (SEV = Société pour l’Equipement des Véhicules) nous en verrons
les conséquences 7 ans plus-tard.
1971: Pour la première fois une journée porte ouverte est organisée le
16 mai pour la visite des usines par le personnel et les familles.
1972: Commence la production d’allumeurs sous licence R.Bosch qui
atteindra une production de 241 000 allumeurs en 1977. FAR reprend, suite à son dépôt de bilan, la Société COSTE à
Lacanche ( Côte d’Or ), 250 personnes environ,
qui fabrique des cuisinières à gaz et électriques et des cuisinières à bois ou
charbon. Elle possède une Fonderie de fonte ‘plate’ à Arc les Gray
(Haute-Saône) avec un effectif de 100 personnes. Les gammes de produits
s’unifient.
1973: Construction de l’usine de
Bourgoin de 10 000 m2.
1974: Grande grève qui donna
lieu à une joute de haut-parleurs : les syndicats avec des mégaphones et
la direction, qui avait installé une puissante sonorisation, répondait.
Cette grève permit d’obtenir la semaine
de 39 heures.Remarques : les grandes grèves donnèrent lieu à des affrontements
épiques pour l’évacuation des ateliers où les acteurs, munis de capots de
cireuses sur la tête, s’affrontaient à coup d’extincteurs. Autre temps !
1976: C’est les débuts des accords Paris-Rhône, Cibié et Ferrodo
1977: Paris-Rhône c’est 3 500 personnes et environ 3 170 000 machines tournantes dont :
- 1 400 000 alternateurs
- 344 000 moteurs à
aimants.
- 24 000
génératrices, c’est le grand déclin de cette fabrication.
-
1 769 000 démarreurs.
FAR absorbe BOURGEOIS à Faverges (Haute-Savoie) : fours
et tables de cuisson encastrables et
matériel professionnel de cuisson. L’effectif est de 125 personnes.La gamme de ces produits permet à FAR de couvrir tous les
besoins du marché. Extension du groupe
Ferodo. SEV absorbe Paris-Rhône et Cibié. Les décisions ne sont plus prises à
Lyon mais à Paris.
1978: Le département des
Appareils Ménagers lance la production du couteau électrique qui sera diffusé sous la
marque Paris-Rhône, et Krups à l’exportation ainsi qu’une machine à laver la
vaisselle dont la production sera limitée à 1 000 unités.
1980: La production des aspirateurs balais représente environ 20 % du
marché français, celle des aspirateurs traîneaux 10 % . Les appareils de
cuisson représentent 5 à 10 % suivant le type de produit. Ferodo devient Valéo le 28 mai 1980. Valéo signifie « je
vais bien » en latin. C’est le nom de la filiale de Férodo en Italie. La couleur verte apparaît sur
tous les documents.
1980: Valéo, comme tous les grands groupes à cette époque, décide
d’abandonner toutes ses diversifications industrielles, pour se recentrer sur
son cœur de métier. Commence le transfert de la production des produits FAR vers
Lacanche. Arrive à Villeurbanne
une production de petits moteurs électriques pou l’automobile.
1981: Recherches de solutions pour:
Bourgeois, Far et le département des Appareils Ménagers.
1982: Dépôt du bilan de Bourgeois, une S A
Coopérative reprend l’activité avec le personnel.Elle produit
actuellement du matériel de cuisson professionnel avec 130 personnes.
C’est aussi le dépôt du bilan de
Far à Lacanche, une reprise partielle des activités est effectuée par la SIL qui produit actuellement avec un
effectif de 120 personnes des cuisinières ‘ haut de gamme’ et des fours professionnels.
Par ailleurs le Groupe implante à Lacanche : Valéo Electronique et
Systèmes de liaison avec un effectif
de 110 salariés.
1982/1984: Valéo arrête la production des Appareils Ménagers à
Villeurbanne. Les lignes de fabrication des aspirateurs sont vendues
à Electrolux. La marque FAR est
reprise par Conforama. Certains outillages de fabrication des cuisinières
partent pour la Tunisie.
1985: Valéo obtient le Grand Prix International de la création
technique pour son démarreur à aimants et réducteur conçu avenue Mermoz.
~ 1987: La fabrication des moteurs est transférée à Châtellerault
(Vienne)
1988: La fabrication des alternateurs est regroupée avec celle de S E V
dans une usine récente à Etaples (Pas-de-Calais)
1989: La fabrication des démarreurs est transférée à l’Isle-d’Abeau
(Isère) dans une usine spécialement construite de 35 000 m².
C’est la fin d’une belle aventure lyonnaise, les sites de l’avenue
Mermoz sont vendus. D’un nombre invraisemblable d’usines, il ne
reste en France qu’une usine de moteurs électriques, une d’alternateurs et une
de démarreurs. Malgré les drames humains, ce fut salutaire pour résister à la
mondialisation à venir. Comment expliquer ce déclin :
1) Les
constructeurs automobiles menèrent une politique pour favoriser la concurrence
en France. Résultats : il y avait 3 fabricants de démarreurs (GM,
Ducellier, Paris-Rhône,) et 5 pour les alternateurs (Ducellier, GM, Motorola,
Paris-Rhône, SEV) Conséquence : des prix au « ras les pâquerettes »
alors que les autres pays ont un ou deux équipementiers.
2) Arrivée
de la concurrence étrangère.
3) Des
investissements de plus en plus élevés. La moindre machine automatique dépasse le million de francs
soit 150 000 euros
4) Ce
n’était pas dans l’air du temps de sous-traiter la fabrication des pièces primaires
pour éviter ces investissements.
Et maintenant un peu de technique sur les produits fabriqués par
Paris-Rhône
Sur un véhicule, la charge de la
batterie est assurée par un générateur de courant qui était jusque dans les
années 1977 une dynamo puis par un alternateur. Ces deux machines sont des
générateurs de courant alternatif dont le mode de redressement du courant
diffère
- Dans
la dynamo: ce redressement est fait par le collecteur du rotor, donc
la puissance est transmise par les 2
balais ce qui limite le courant à 20 à
30 ampères. D’autre part il n’y
a pas de débit au ralenti moteur, une génératrice donne 10 ampères à 1700 t/min
ce qui est inacceptable avec la
ribambelle d’accessoires de nos voitures actuelles.
- L’alternateur c’est l’apparition des diodes au
silicium qui permit son développement. Le redressement est réalisé par un pont de 6
diodes sur un alternateur triphasé, qui est fixé sur le palier arrière. Le
courant est débité par le stator et le rotor sert à créer le champ magnétique
d’excitation avec un courant de 3 à 6 ampères. Cette machine débite 10 ampères
à 1200 t/min. Avec un rapport générateur/moteur d’environ 2 nous voyons qu’au ralenti moteur la plupart des accessoires
seront correctement alimentés par l’alternateur. Comme le courant principal ne
passe plus par les balais le débit d’un alternateur peut atteindre de 50 à 100
ampères suivant les modèles. D’autre part sa puissance massique est plus
élevée. Toutes ces qualités expliquent la disparition des dynamos.
- Régulateurs: la dynamo ou l’alternateur sont
pourvus d’un régulateur pour maintenir constant la tension de charge d’une
batterie à 14.5 volts pour une batterie de 12 volts. Cette régulation se fait
en
réglant le courant du bobinage d’excitation. A l’origine cette fonction fut
réalisée par un régulateur vibrant à contacts. Cette petite boîte noire fut un
chef-d’œuvre d’astuces pour maintenir la tension constante à 0,2 volt près
quels que soient le débit et la vitesse du générateur, sans oublier la compensation
en température de cette tension. Maintenant cette fonction est faite par
l’électronique, de séparé le régulateur est devenu incorporé à l’alternateur.
- Démarreurs : c’est un moteur série qui se
compose d’un bobinage inducteur fixe, d’un rotor alimenté par 2 balais, d’un
lanceur qui viendra s’engrener sur la couronne moteur pour assurer le démarrage
du véhicule et d’un contacteur qui a 2 fonctions : alimenter le démarreur
et permettre l’engrenage du lanceur dans la couronne. Son évolution sera :
- Démarreur à réducteur : dans les années 1970 les Japonais
présentent aux constructeurs français ces nouveaux démarreurs qui divisent le
poids par 2 et l’encombrement. A titre d’exemple un démarreur de 115 mm de
diamètre passera à 90 mm et son poids de 11 kg à 5.6 kg. Devant une perte de
marché assurée Paris-Rhône lance, en 1985, ses premiers démarreurs à réducteurs.
Démarreur à réducteur avec des
aimants et un collecteur plat :
Naissance du D6RA avec D comme
démarreur, 6 pour 6cm de diamètre, R pour réducteur et A pour aimants. Destiné aux véhicules début et moyen
de gamme, il fut conçu avenue Mermoz
dans les années 1984/1985 et reçu le grand prix international de la
création technique en 1985. C’est le fruit d’une organisation en équipe
remarquable avec l’introduction d’un groupe de travail rassemblant les études,
les méthodes et la fabrication. Ce qui changeait des habitudes
classiques : le bureau d’étude conçoit, les méthodes prévoient la
fabrication et la dite fabrication se débrouille ! Les
avantages de ce démarreur sont importants :
- plus
performant à froid, grâce aux aimants
- le
collecteur à plat permet d’automatiser sa fabrication
- gain
massique très important : 2,75 kg au lieu de 5,6 kg
Bibliographie :
- Usine Nouvelle supplément du 13/2/1986
- Mémoire de travail : ouvrières à l’usine Paris-Rhône n°3
- 2004
- Histoire de la Société
de Paris et du Rhône de Pierre-Lucien Pouzet
- La Grande Aventure automobile lyonnaise de Pierre Lucien Pouzet
nous contacter
|